Since we built the automatic DIY pick and place machine, one aspect of the build which has always caused us problems is the speed at which Mach3 communicates with the SmoothStepper Ethernet board and the lack of ability to send more than one command to the stepper motors at a time.
The result of this limitation is that the machine can only make single moves with a short pause between each axis move which is causing a lot of delays when building circuit boards.
Another major limitation is the lack of real-time closed-loop feedback which Mach3 doesn’t support from linear encoders which results in the stepper motors losing their position after placing multiple components.
After a lot of research, we decided to order a KFlop motion controller from dynomotion.com/KFLOP.html which is a standalone motion controller with outputs for up to eight axis and other IO and PWM inputs and outputs. The KFlop supports optical and magnetic linear encoders and we are planning to install linear encoders on the X and Y axis on the pick and place machine.
At the moment the machine is using a SmoothStepper Ethernet motor controller via Mach3 and a custom motor controller board with three microcontrollers which connect to the host PC via USB and control the feeder system, air and vacuum valves and LED lighting for the cameras.
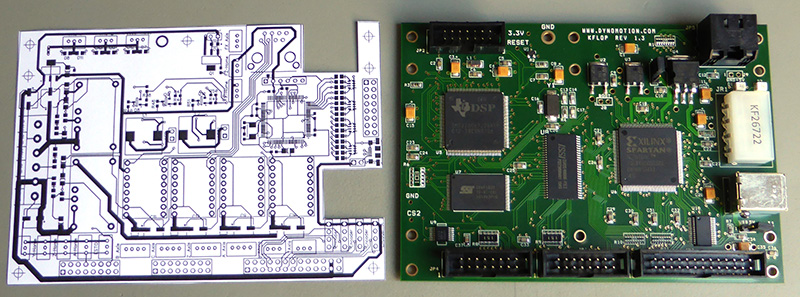
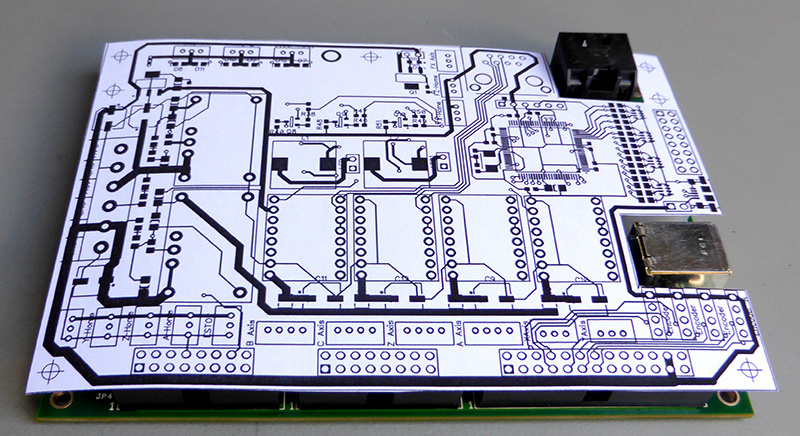
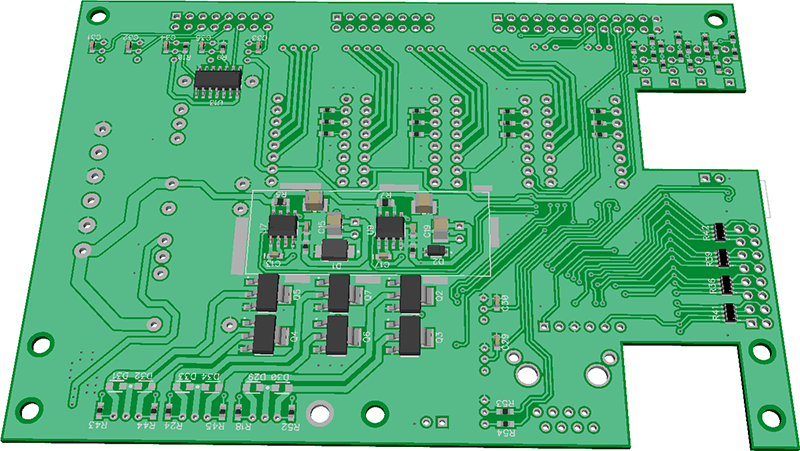
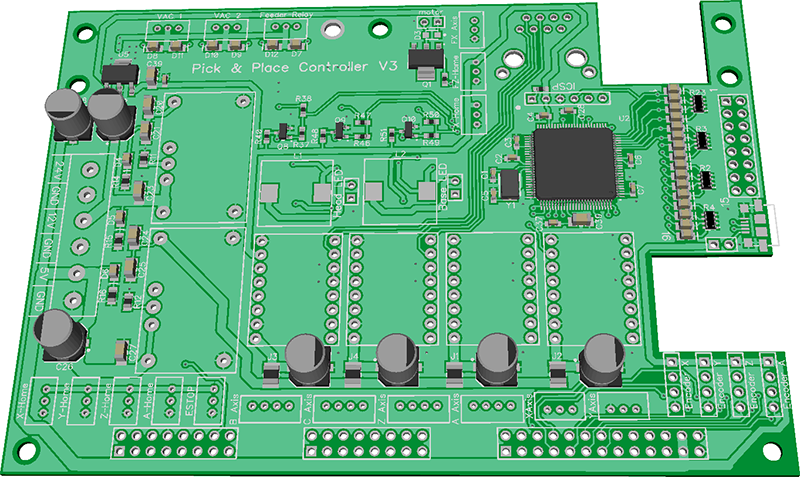
The new KFlop board will connect to a new controller board which we have designed in Diptrace (see 3D mock-ups on right) and this will have a single Microchip PIC32 processor which will replace the previous board’s functionality and also have an additional 16 IO channels to drive 16 valves for a possible feeder system upgrade we have planned.
We will add a new post when the PCB arrives and is up and running on the pick-and-place machine.
Comments